Documentation >
MAC-PAC Reference Library >
Manufacturing >
Shop Floor Control >
Key Concepts and Procedures >
Labor Requirements Generation and Order Scheduling >
Lead Time Calculations
Lead Time Calculations
An operation's scheduled lead time is the sum of setup and run time, which is offset for and move and queue time when necessary.
Setup time for an operation is taken directly from the labor requirements record, where it is defined in hours.
Run time for fixed time operations is taken from the piece rate*, which is defined on the labor requirements record.
Run time for operations with variable run times must be calculated according to one of the following formulas:
· In a machine-paced workcenter, the run time (in hours) equals:
Piece Rate * x (Order Quantity - Cur Cum Scrap**)
Number of Machines
· In a labor-paced workcenter for a non-crew operation, the run time (in hours) equals:
Piece Rate* x (Order Quantity - Cur Cum Scrap**)
Number of Persons
· In a labor-paced workcenter for a crew operation (independent of number of persons), the run time (in hours) equals:
Piece Rate* x (Order Quantity - Cur Cum Scrap**)
Operation lead time is then calculated by adding the run time to the setup time; the sum is then divided by the hours per day for the workcenter in which the operation takes place. The final result is the total elapsed time (in days).
* Piece rate is a plant specific option. It may be defined as hours per piece or pieces per hour. If the latter is used, the piece rate is inverted before these calculations are performed.
** Cumulative scrap is maintained on each labor requirement record. The scrap figure in this calculation represents the total quantity scrapped at all prior operations in the routing; scrap from the present operation is excluded.
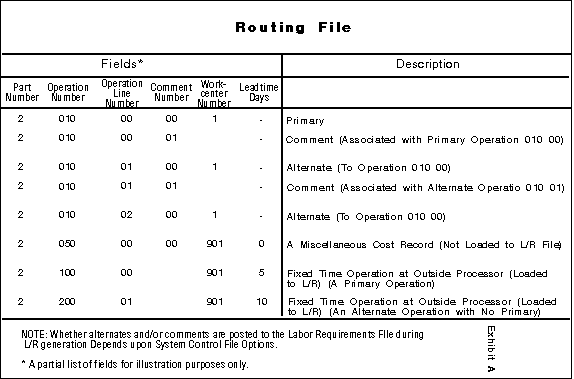
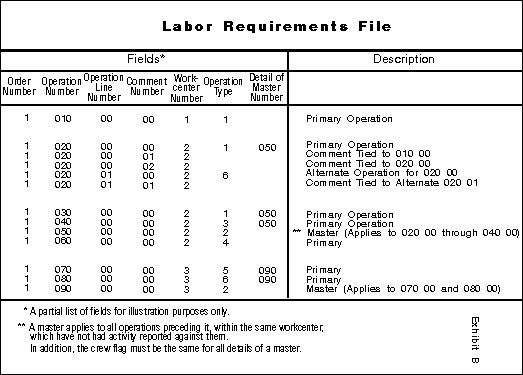
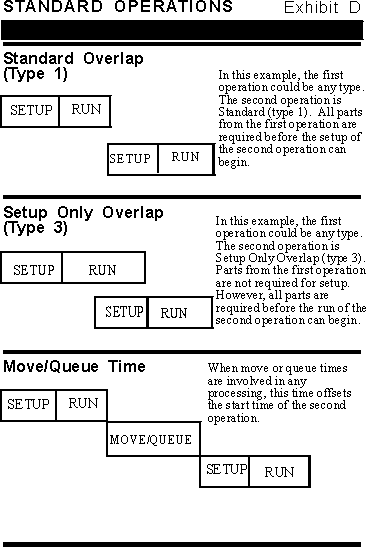
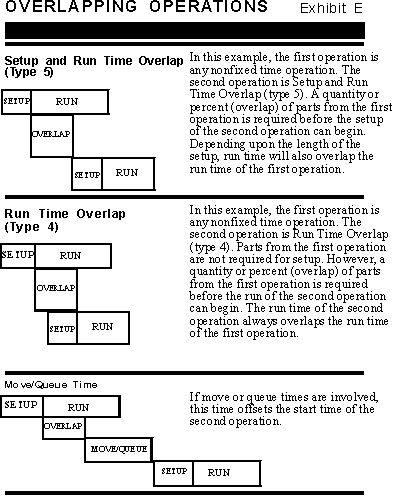
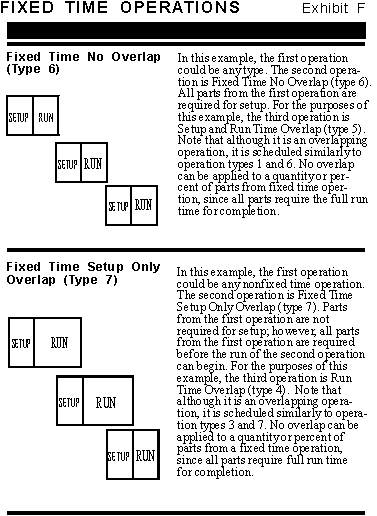
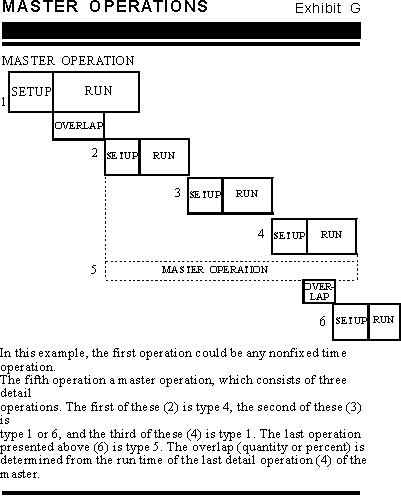