Documentation >
MAC-PAC Reference Library >
Distribution >
Order Processing >
Key Concepts and Procedures >
Order Release and Picker Information >
Blanket Shipment Scheduling
Blanket Shipment Scheduling
The blanket order shipment scheduling feature allows you to establish a timetable for multiple shipments that are to be made against an existing blanket sales order. Each shipment schedule line may have varying characteristics defined in terms of the shipment dates, quantities, warehouses from which inventory will be shipped, and customer locations to which inventory will be shipped.
The order quantity of a blanket order line records the total quantity to be shipped to the customer over a period of time. A shipment schedule establishes the dates, quantities, and locations for multiple shipments to be applied against that ordered quantity. Shipment scheduling information is entered through the Sales Order Maintenance conversation on the Blanket Shipment Schedule screen (OP115S02). This can be done when the order is entered or can be maintained as requested by the customer. A sample of this screen is shown below. For specific field validation rules, refer to the Screens section of this manual.
WILLIAMS CO 001 ORDER PROCESSING FRF 5/05/92
DSP01 WHS BEL SALES ORDER MAINTENANCE SCHED
Order 001486 00 Type BLK
Customer C01 BRUNOT MOTEURS 1 Order Status OPN
Part Number BOLT-100 Order Date 05/13/92
Line Number 002 Line Order Qty 275.000
Ship Date 05/15/92 Total Sched Qty 250.000
L Scheduled Src Ship
S Prm Ship Quantity Whs To
O 05/20/92 100.000 BEL 001
O 05/25/92 150.000 BEL 001
F2=Command F4=Prompt F12=Cancel F15=Rekey Data
|
Blanket Shipment Schedule Screen (OP115S02)
To use shipment scheduling, the Sales Order Maintenance Function Select screen (OP100S01) must have the Blanket Scheduling field set up to allow shipment schedules. This can be done manually during each Sales Order Maintenance conversation or by using the default value established on Reference File category 413.
Shipment Scheduling Set-Up Options
The default value for the blanket scheduling option is established on Reference File category 413, Order Processing System Defaults. Valid values for the option are either Y (Yes, establish blanket shipment schedules) or N (No, do not establish blanket schedules--shipments will be determined based on the release interval and number of releases requested). The value established on this Reference File automatically defaults to the Blanket Scheduling field on the Sales Order Maintenance Function Select screen (OP100S01). This value may be overridden for each blanket sales order at entry time. Once a sales order has been successfully added, the Blanket Shipment Scheduling option cannot be changed.
Choosing whether to use blanket shipment scheduling depends on the requirements of your customer. If the blanket shipment scheduling option is not used (Blanket Schedule flag = N), the shipment schedule is defined in terms of the number of releases and release interval, which are both entered on the Sales Order Maintenance Function Select screen (OP100S01). This method assumes that the customer wants an even schedule of shipments; for example, if 100 units are desired and the number of releases is 5 and the release interval is 10 days, then your customer would receive 5 shipments of 20 units every 10 days. This method requires less data entry, but it is only suitable when regular shipments are desired.
On the other hand, if the shipment scheduling option is used (Blanket Schedule flag = Y), you have the additional flexibility of entering several shipment specifications. Using these specifications, you can define a schedule with varied dates and quantities as well as customer locations. This feature requires you to enter shipment scheduling information for each scheduled shipment.
Shipment Scheduling Information
Several fields determine the characteristics of a shipment line. These fields are entered separately on the Blanket Shipment Detail screen (OP115S02) for each shipment line. They consist of:
· Line Status - indicating whether a release has been generated to cover the shipment line.
· Promised Ship Date - the date inventory is to be shipped.
· Scheduled Quantity - the quantity to be shipped.
· Sourcing Warehouse - the warehouse from which inventory will be shipped.
· Ship-to Customer Number - the customer location to which inventory will be shipped.
The Line Status code indicates the status of the shipment. As long as a shipment release has not been generated, the status of the scheduled shipment will remain O (Open). Once a blanket order release has been generated, the system will change the scheduled line status to R (Released). The status may also be set to C (Closed) to cancel a scheduled shipment. Scheduled quantities can be maintained only for open shipment schedule lines.
The Promised Ship Date field identifies the date that each scheduled shipment should be shipped to the customer. The promised ship date is used by the Automatic Order Release program (OP630E) to determine when a release should be generated for a given shipment. A release will be generated when the promised ship date on the scheduled shipment is within the shipping lead time of the sourcing warehouse. Releases may also be created through the Blanket/Backorder Release window (BKTBOS02) which is accessed from maintenance code '4' on the Sales Order Maintenance Function Select screen.. The data entered in this window is validated by OP630E and if a release is generated, it will be processed through Sales Order Maintenance as if you had requested maintenance on it.
The Scheduled Quantity field facilitates multiple shipments against one blanket sales order line. The scheduled quantity indicates the inventory quantity to be shipped to the customer, as entered on each shipment line. A total of all the shipment quantities on the schedule will be summed in the Total Scheduled Quantity field. If this total exceeds the Line Order Quantity for the sales order, a warning message will be displayed before the shipment schedule can be confirmed.
The Sourcing Warehouse field is used to indicate the warehouse from which the inventory will be shipped. Multiple sourcing warehouses accommodate geographic or time/inventory restraints. This field can be changed at any time until the release has been shipped.
The Ship-to Customer field indicates the customer's destination for the scheduled shipment. This field allows you to send several shipments of different quantities to multiple customer locations.
Blanket Order Releases
A blanket order defines the items and the total quantity that will be shipped over a period of time in multiple shipments. Blanket order releases must be generated to ship against blanket orders. The following illustration describes the flow required for the Order/Release/Shipment process. Once a blanket order (parent order) has been created, whether it has a shipment schedule or not, a order release (child order) must be generated to reserve the maximum available inventory amount at the warehouse. This can be done automatically using the Automatic Order Release program (OP630E) or the Blanket/Backorder Release window (BKTBOS02) which is accessed from maintenance code '4' on the Sales Order Maintenance Function Select screen.. OP630E will be used to generate the release, and if successful, the Sales Order Maintenance program (OP100E) will retrieve the newly created sales order header records, change the maintenance code to '2' (change), and process the blanket or backorder release as if you requested maintenance on it. If OP630E cannot create a release, you will receive an error message.
Once a release has been generated, a shipment request is filled and sent to the customer. Shipment information is then recorded against the appropriate blanket order release (child order) through the Shipping/Billing conversation. It will also roll up to the blanket sales order (parent order).
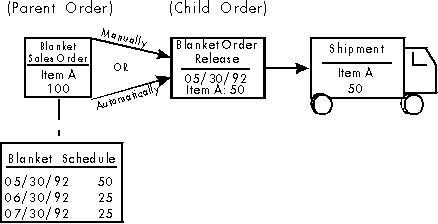
Order/Release/Shipment Process
If blanket orders use a shipment schedule, releases are generated (either automatically or manually) for each unique combination of ship-to customer, sourcing warehouse, and promised ship date. A blanket order release will be generated by the Automatic Order Release program (OP630E) if the promised ship date falls within the shipping lead time for the sourcing warehouse. Furthermore, if additional shipments are requested, they can be generated at any time using the Blanket/Backorder Release maintenance code option on the Sales Order Maintenance Function Select screen. For more information about either method of generating releases, refer to other key concepts in this manual.
Considerations
Regardless of whether blanket scheduling is used, inventory reservation does not occur until a blanket order release is created.
Overscheduling is allowed for blanket shipments. The total quantity scheduled can exceed the original order quantity for the line.
At the time of BOL generation, the next available Bill of Lading Number will default for the specified company/location from Reference File category D91, Next Bill of Lading Number. Once established, this number cannot be changed.